Engine protection for VLSFO's
VPS Whitepaper by Stanley George, Ade Allman and Paul Parkinson.
Summary
Compliance with the 2020 IMO 0.5% sulphur cap has driven the introduction of Very Low Sulphur Fuel Oils (VLSFOs) since September 2019. During this period VPS has identified significant engine damage arising more than 40 vessels with very similar faults resulting in serious operational issues. This White Paper details the investigation carried out by VPS into 15 of these incidents. It confirms that the damage to engine components is due to abrasion by hard calcium deposits arising from additives in the Lubricating Oil (LO). The underlying cause is inadequate LO formulations which have been poorly matched to the VLSFOs.
The combustion of VLSFO produces much lower acid concentrations due to reduced S levels in marine engines as compared to traditional Heavy Fuel Oil. This has required a change in formulation of the cylinder LO, specifically the alkalinity (Base Number, BN) which is used to protect the cylinders by neutralising the acids produced by fuel combustion. Suppliers have recommended ship operators to use 40BN cylinder oil for use with VLSFOs (rather than 70BN recommended for use with HFO).
VPS has identified excessive liner wear on the cylinder units of two-stroke engines used for main propulsion on vessels since the introduction of VLSFOs. This damage to engine components has a detrimental impact on vessel operability and has been investigated in this report. The engines affected were not limited to any specific OEM but from many of the major engine makers in the marine industry. In all cases VLSFO fuel quality was tested and found to be acceptable and the original cylinder oil that was used was grade 40BN (Base Number) supplied from most of the key suppliers.
The investigation identified that the reserve BN in the cylinder oil was not being utilised to neutralise the acids formed during the fuel combustion process as is its purpose. This resulted in calcium compounds being deposited on the piston top, which became hard and abrasive causing liner wear, liner scuffing and piston ring breakage resulting in serious operational issues.
A number of preventative actions may be taken by ship operators using VLSFOs to protect engines and avoid operational issues arising from excessive liner wear. Primarily, undertaking VPS Cylinder ScrapeDown Analysis will identify if an adequate LO formulation is being used, which may be further confirmed by a VPS Sweep Test. In addition to this, the ship operator should closely monitor engine operation during introduction of new VLSFO fuel and changeover of VLSFO to MGO and MGO to VLSFO when entering/leaving ECAs.
1. Introduction
MARPOL Annex VI global fuel sulphur cap to 0.50% came into force on 1 January 2020 and has resulted in a significant increase in the use of Very Low Sulphur Oil (VLSFO) fuels as illustrated in Figure 1. VPS has seen a significant increase in problems leading to a detrimental impact on operability correlating to this increased use of VLSFOs. A number of engine-related problems are discussed here including excessive liner wear, piston breakage and hard deposit formation on the piston area. The introduction of VLSFOs has also resulted in fuel problems such as excessive sludging, low flash point, low shelf life, cold flow properties including high Wax Appearance Temperature (WAT) which are discussed elsewhere.
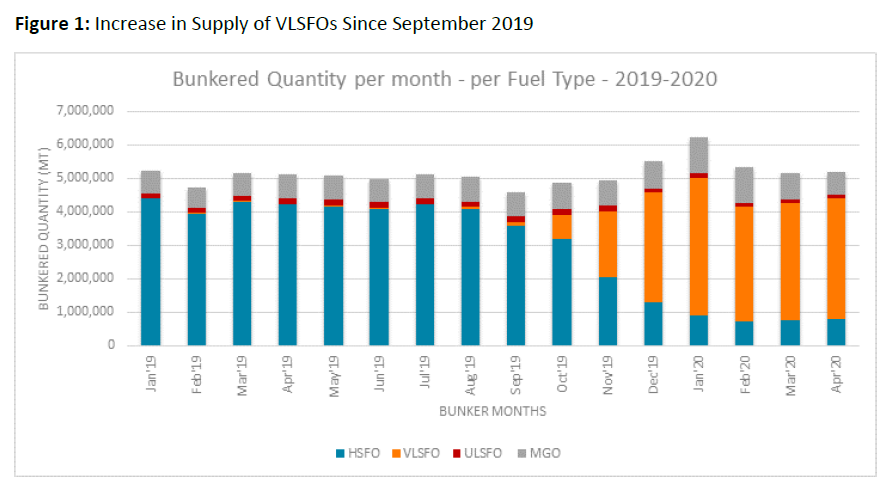
VPS has identified multiple cases of reddish or white/grey coloured deposits formed on the surface of engine components since the introduction of VLSFOs (see Figure 2). These deposits were found on the piston top, piston crowns and underside of the cylinder heads and were linked to excessive wear of cylinder liners, liner scuffing and broken piston rings. The deposits were found to be very hard, requiring the use of power tools to remove and clean. VPS discovered that two-stroke engines were more susceptible to these types of damage.
Figure 2: Red tinge on piston top with evidence of wear (Note: red coloured deposits adhered to the piston top that was found during the dismantling of the cylinder unit for carrying out breakdown maintenance).
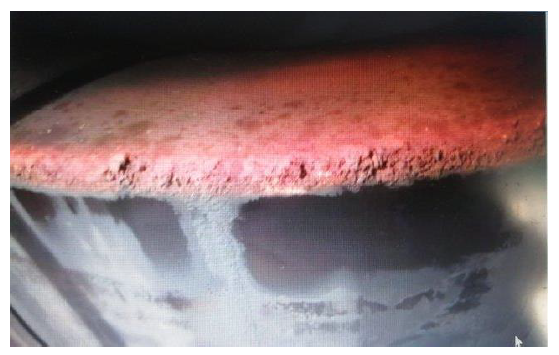
2. Summary of Reported Incidents
More than 15 incidents of engine damage resulting from excessive liner wear were investigated by VPS from October 2019 to April 2020. Table 1 summarises these incidents, which were not restricted to any particular cylinder oil supplier or any engine make.
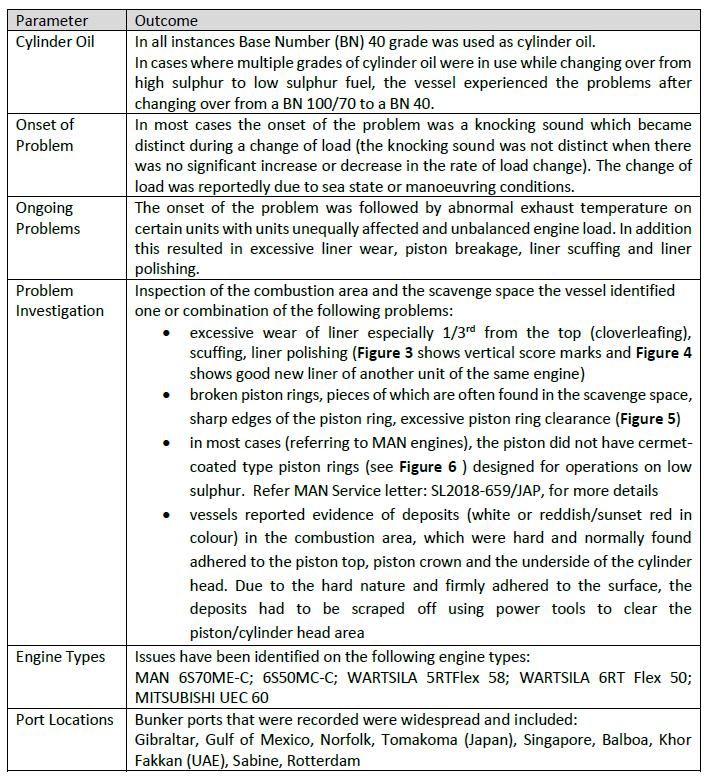
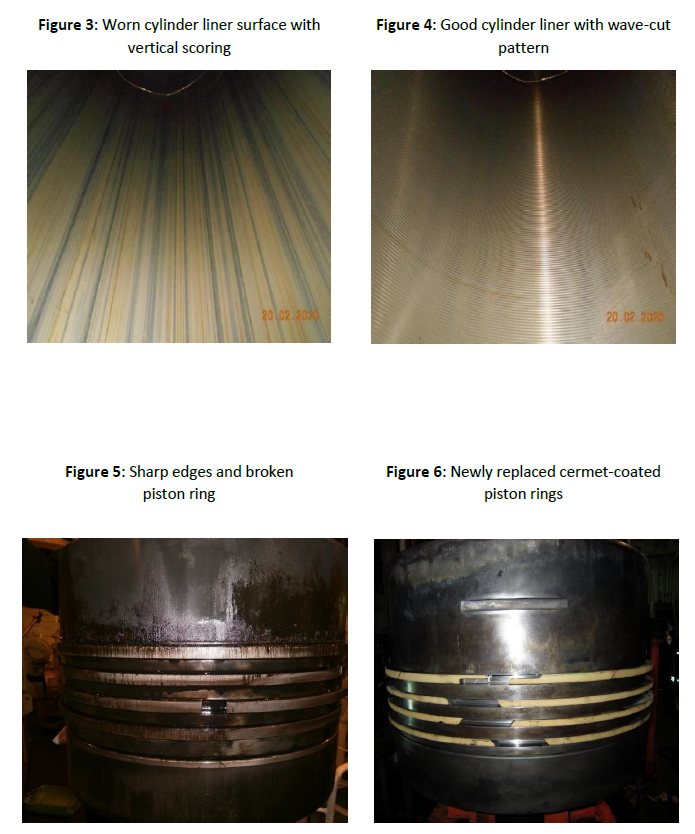
3. Investigation
A thorough investigation into excessive liner wear and the operational issues this caused was carried out by VPS. This included testing a number of fuel and oil samples taken from these incidents, as well as analysing sludge and hard deposits taken from damaged engine components including piston top, piston crown and piston rings. This investigational analysis is summarised in Table 2. The investigation also involved reviewing ship’s data, reference documents and reports including work carried out by Original Equipment Manufacturer (OEM) or third party contractors.
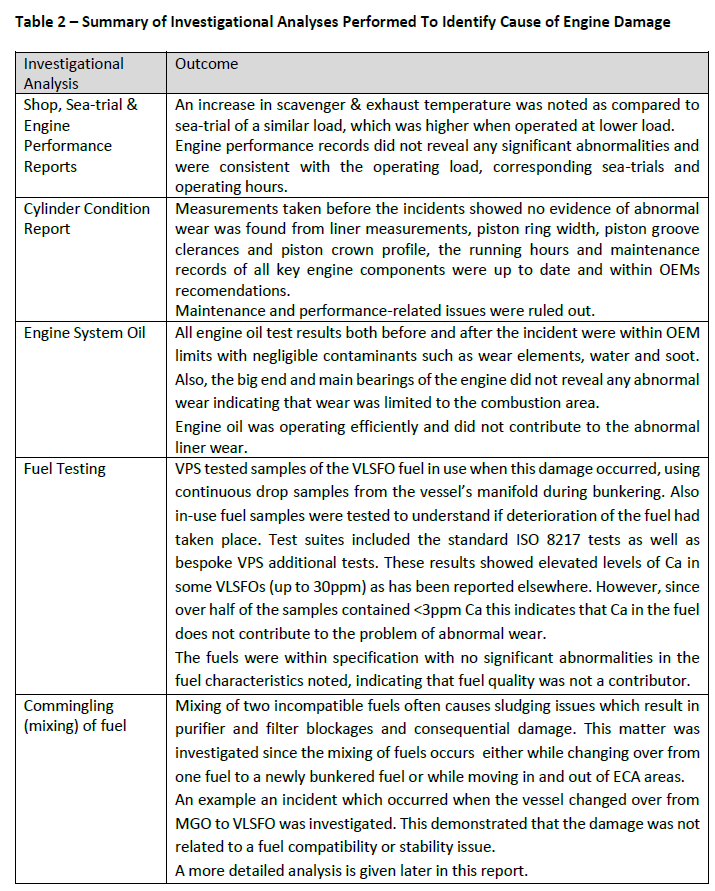
Scavenge Port Inspection Analysis Photographs
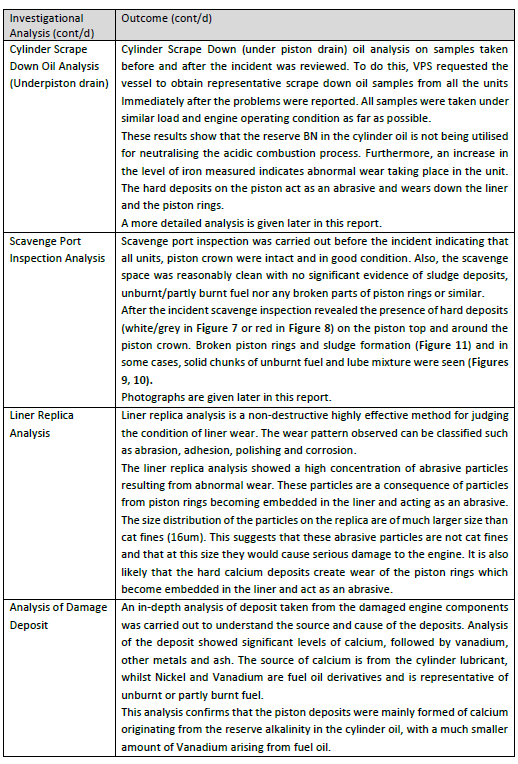
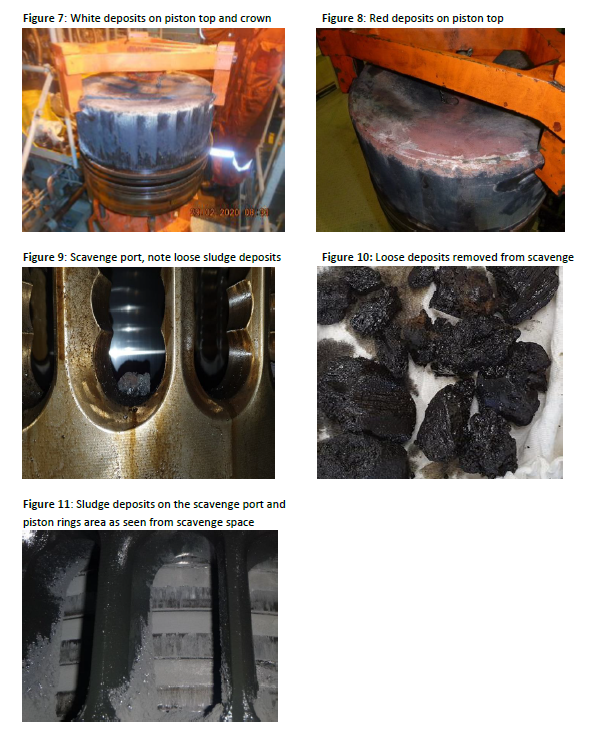
3.1 Details on Investigation Into Commingling (mixing) of Fuel
Mixing of two incompatible fuels often causes sludging issues which result in purifier and filter blockages and consequential damage. This matter was investigated since the mixing of fuels occurs either while changing over from one fuel to a newly bunkered fuel or while moving in and out of ECA areas. During such periods the mixing of fuel to some extent is unavoidable: such as un-pumpable, fuel remaining in the bottom of the tank, fuel remaining in the fuel oil line leading from service tank to the engines, filters, mixing columns etc.
An example an incident which occurred when the vessel changed over from MGO to VLSFO was investigated. Test results of both the fuel are stated in the Tables 3 and 4.
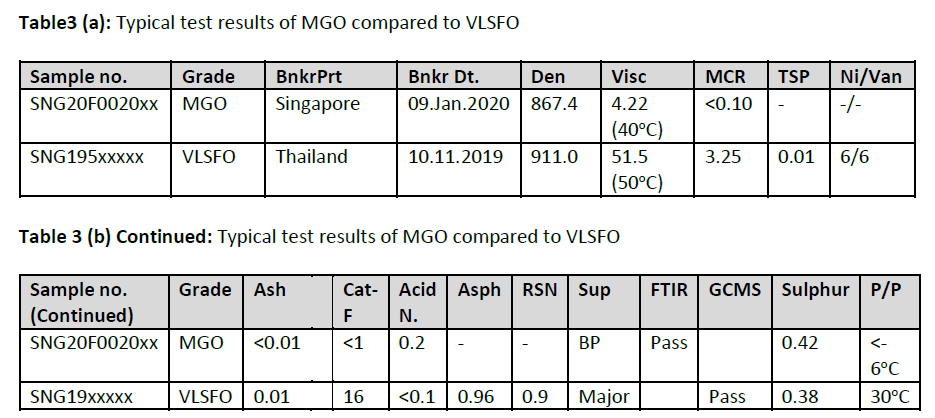
During the changeover the vessel had to mix MGO with VLSFO. The TSP and reserve stability (RSN) of the VLSFO was very low indicating this fuel was stable. After blending the vessel did not experience sludging issues nor there were any reported problems with the purifiers and filters. VPS also carried out a compatibility test of the above two fuels which showed that there are no compatibility issues. This demonstrated that the damage was not related to a fuel compatibility or stability issue.
3.2 Details on Cylinder Scrape Down Oil Analysis (Underpiston drain)
A typical example of scrape down analysis results are shown in Table 5 below. In this example the vessel changed over from a high sulphur fuel to a VLSFO towards the end of 2019 in preparation for the IMO 2020. During this changeover, the vessel also changed the cylinder oil grade. Samples were taken before the incident, during the start of the incident as indicated in the table below.
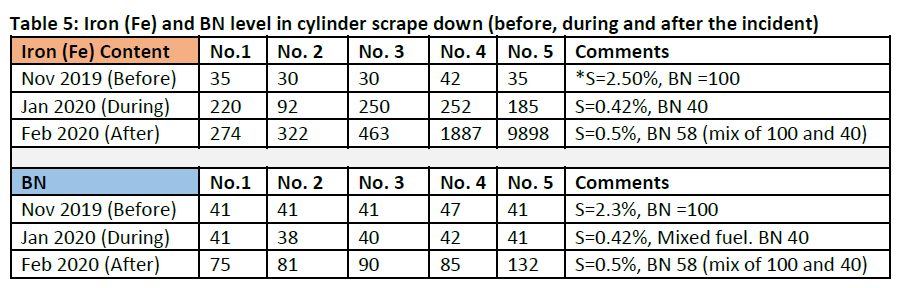
Cylinder scrape down – Before the incident (Cylinder feed rate ≈ 1.15 g/kWh)
The Iron (Fe) content in all the 5 units appears satisfactory. Considering the cylinder oil in use, 100 BN and the fuel sulphur of approximately 2.50% the BN in the cylinder scrape down oil appears to be satisfactory and within limits.
*S = 2.50% - There was some commingling involved between fuels with sulphur = 2.30% and another fuel with sulphur = 2.7%, bunkered at different ports.
Cylinder scrape down – During the start of the incident (Cylinder feed rate ≈ 1.35 g/kWh)
The Iron (Fe) content in all the 5 units appeared to be elevated. See Table 6 for typical ferrous content in scrape down oil based on engine size. Considering the cylinder oil in use is a 40 BN and the fuel sulphur of approximately 0.40% (mix of S-0.42% and S-0.38%), the BN in the scrape down oil appears to be significantly high and close to or marginally above the new oil value.
Cylinder scrape down – After the incident (Cylinder feed rate ≈ 1.5 g/kWh)
There is a significant sharp spike in the iron content in Unit no.5 followed by unit no.4 and unit no.3 This is backed up by the high PQ index indicative of wear. This indicates abnormal wear in unit nos. 5 and 4. Unit no.3, 2 and 1 are following suit. High reserve BN on all units are observed. Particularly very high BN was observed on unit no.5 (132), which incidentally also shows the highest level of iron content at 9898 ppm. Similarly, unit no. 4 (85), unit no. 3 (90) and unit no.2 (81)
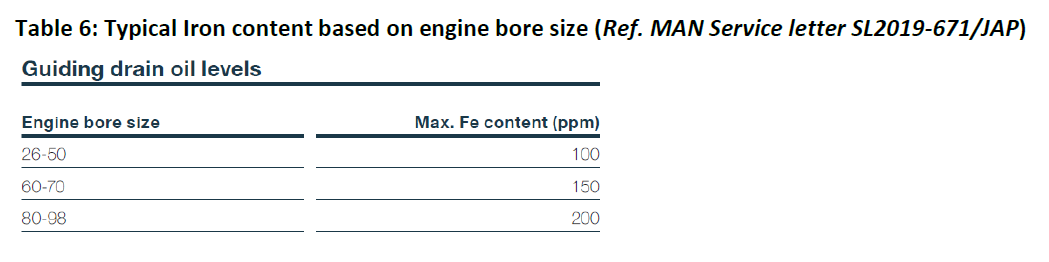
3.3 Liner Replica Analysis
Replica measurements were carried out from vessels as part of this investigation. Photomicrographs of the replicas taken from Main Engine Cylinders show that particles of catalytic fines are apparent on the examined surfaces as in Figure 12 below. Closed/partially open graphite flakes can also be seen. The heavy abrasive wear evident on the examined surfaces is in line with what could have been caused by hard catalytic fines particles. It should be noted that in units where excessive wear was recorded the particles’ areal density reached at instances ~2000 particles/cm2. Bearing in mind that the typically acceptable limit by engine manufacturers is ~200/cm2, it becomes apparent the scale of the problem. Also, particularly large diameter particles were evident, above 20μm in diameter at instances, which could certainly contribute to very fast liner wear rates.
Since catfine particles are relatively hard as compared to the liner surface condition it is not uncommon to find these particles embedded into the liner surface over the lifetime of the operation. Catfine particles can also cause abrasive wear of the piston rings and sharpening of the edges. However, it should be noted that the fuel in use had <2 ppm catfines at engine inlet suggesting that catfines were not the source of this abrasion problem. Furthermore, distribution of the catfines and other particles identified from the replica show an overall representation of the liner surface condition over its lifetime of operation. As such it is likely that the catfines were present from a previous batch of fuel that was in use immediately before the replica being taken.
The size distribution of the abrasive particles was carried out to further learn the effect of wear. The replica was carried out on the worst affected cylinder liner. The histogram presented in Figure 12 shows that most particles were in the range between 12 μm and 16 μm in diameter. Particles with diameters below ~8 μm are usually not found embedded in the liner surface and not considered harmful for the engine operation. Particles with diameters above ~8 μm become a serious threat to the normal engine operation. The larger the size, the more detrimental damage to the liner can be expected and Figure 13 shows that 80% of the particles were >8 μm.
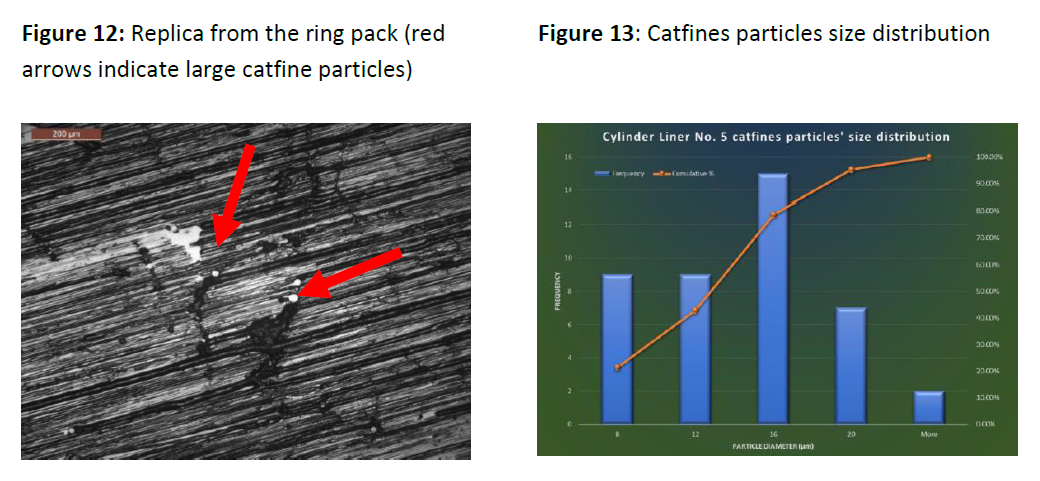
3.4 Analysis of Damage Deposit
One of the common features noted in this type of damage was the presence of deposits arising on the surface of pistons. The deposit was concentrated on the piston head and in areas around the piston crown. The deposits were hard in nature and were either white/grey as in Figure 14 (which shows the white deposit after the deposit was mechanically removed from the piston) or reddish coloured as in Figure 15 (deposit on the piston head). Samples of these deposits were analysed for elemental composition.
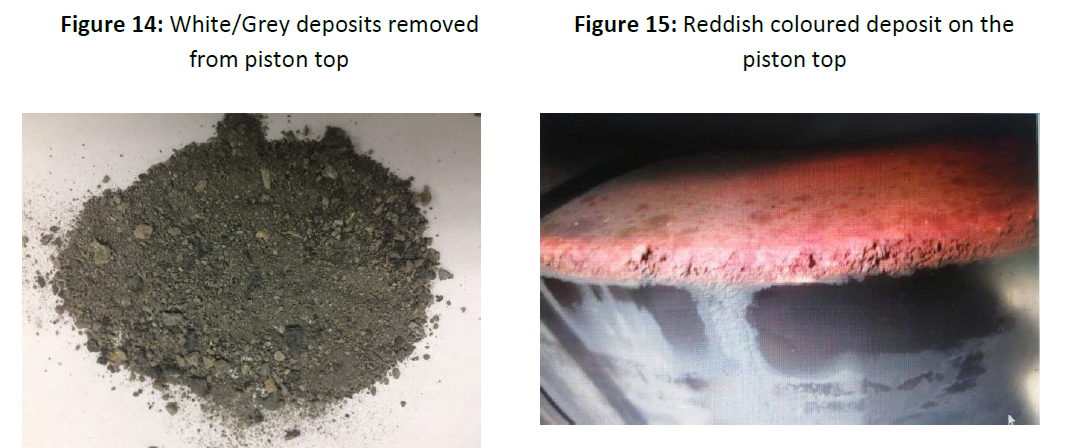
There were also some instances when the vessel faced severe sludge formation (hard sludge) in the purifier followed by excessive liner wear and breaking of piston rings. Therefore samples of the sludge taken from inside the fuel oil purifier were also analysed for elemental compostion. Comparison of the elemental analysis of the piston desposits with the purifier sludge is shown in Table 7. This clearly shows that the piston deposits were mainly formed of calcium originating from the reserve alkalinity in the cylinder oil, with a much smaller amount of Vanadium arising from fuel oil. Furthermore, the increase in iron content in a cylinder scrape down oil analysis indicates abnormal wear of that cylinder unit and piston rings.

4. Conclusions
The investigation has shown that the engine damage is not directly related to the fuel quality, engine operating conditions or engine maintenance. Furthermore, the damage is not due to a compatibility issue caused due to mixing of non-compatible fuels. This is important because there are frequent fuel changeovers from VLSFO to MGO and back again whilst travelling through ECAs.
This investigation has shown that the engine damage is related to the LO used, specifically in combination with the particular VLSFO. The variation in constituents of VLSFOs has the potential to impact on combustion zone deposit formation. This is handled by the lubricants and the additives that are present in them. Cylinder oils previously developed for use with fuels with a sulphur content of up to 1.5% may not provide the performance required to handle VLSFOs that are currently supplied in the marine industry. Currently suppliers recommend 40BN LO for use with VLSFOs. However, the results of this investigation suggest that a 20BN oil may be more appropriate for some VLSFOs, depending upon the specific residual content of the fuel. Selection of the most appropriate LO can be made based on VPS scrape-down analysis. Furthermore, the feed rate of the LO is important and this can be optimised by the VPS sweep test.
The reserve BN in the cylinder scrape down analysis was higher than expected when compared to the grade of cylinder oil and the sulphur content of the fuel in use. This indicates that the BN in the new oil is too high, not compatible or the cylinder lube oil feed rate is too high. This causes excess calcium in the LO forming the build-up of deposits.
Engine damage deposits were shown to be hard Calcium carbonate (CaCO3) deposits, which causes bore polishing, liner scuffing and excessive liner wear. These deposits were formed from excess calcium in the LO not being used up to neutralise the acids arising from the fuel combustion process. These deposits formed in the combustion space that overtime forms hard deposits on the piston top whilst in operation.
Appendix – Actions to Protect Engines When using VLSFOs
1. Engine operations are closely monitored, especially during change-over from MGO to VLSFO or from one VLSFO to another.
2. Select the correct cylinder lubricating grade. Typically, 40 BN cylinder oil while using VLSFO (≤0.50%) 15- 25 BN when using ULSFO (≤0.10% fuel).
3. Mainly to look for any knocking sound, load unbalance, high exhaust temperature deviation.
4. Regular scrape down analysis is a great tool to identify the cylinder condition, but sometimes it may be late for the vessels to react by the time they get the analysis results from the lab. Although this is not a substitute for sending samples to the lab, procuring an onboard kit for measuring iron and BN is recommended. As soon as any changes are done to cylinder lubrication, the vessel should take a Cylinder Scrape Down sample from each of its units and analyse it so that immediate action can be taken, following which the same subsamples should be sent to the lab for a detailed analysis.
5. In case a unit shows high ferrous content in the scrape down oil, before adjusting the feed rate make sure the reserve BN in the scrape down oil is within the expected range (typically between 20 to 30 BN when using a 40BN oil on a 0.50% fuel). Increasing the federate when the reserve BN is already high (> 30BN while using a 40 BN cylinder oil on a 0.50% fuel) may result in excessive calcium formation that forms hard deposits on the piston head and surrounding areas. This would then result in increased deposit formation, consequently, excessive wear of the liner, sharp piston ring edges, broken piston rings and scuffing of liner can occur.
6. It is often seen that the vessel as a precaution, increases the cylinder oil feed rate of the affected unit when a high iron content is recorded in a Cylinder scrape down analysis report (or analysis using an onboard kit). The intention being to increase the hydrodynamic lubrication to reduce wear. However, statistics indicate that increasing the cylinder feed rate, when the remaining BN in the scrape down analysis is high (>80% of the new oil value) has worsened the situation. In such cases, the amount of deposit formations has increased with a rapid spike in the ferrous content consequently excessive wear of the liner, sharp piston ring edges and scuffing of the liner.
7. The feed rate should not be altered without considering the other parameters, mainly BN and Ferrous content in the cylinder scrape down oil. The optimum feed rate can normally be identified by carrying out a ‘Sweep test’1. The ferrous content found in a cylinder scrape down analysis must be considered in conjunction with the reserve BN content. See Table 6 for typical ferrous content based on engine size. The amount of calcium that is found in the cylinder scrape down analysis normally represents the reserve of alkalinity present in the remaining oil after cylinder oil has performed its ‘functions’. With regards to this discussion, the ‘function’ referred is to neutralise the acidic compounds of combustion. The remaining BN will, therefore, depend on various factors such as fuel sulphur content, load on the engine, the grade of the oil in use and of course the cylinder feed rates.