Learning curve of VLSFO characteristics
Article published in Bunkerspot (June/July 2020)
Steve Bee looks at the story so far in terms of the characteristics and behaviour of the new breed of VLSFOs.
There is always an element of fear when stepping into the unknown, which usually results in acting cautiously and even offering an element of resistance. For the shipping industry, 1 January 2020 was certainly a step into the relative unknown with respect to IMO 2020 and the consequential fuel considerations for ship owners and operators – and the key question being which strategic decision would be the best for their business in a world of more stringent environmental regulations?
For over 50 years, marine fuels had predominantly been limited to residual heavy fuel oil (HFO) and distillate grades of marine gasoil (MGO). Whilst improvements in crude oil refining and MARPOL Annex VI legislation altered those two marine fuels to some degree over the past years, with the implementation of IMO 2020 the purchasers and users of marine fuel now had a more complex choice to make, summarised as:
1. Use only MGO, historically the most expensive fuel to use.
2. Or, use HFO in combination with installing exhaust-gas-cleaning-systems onboard vessels, which come with their own considerable investment commitments.
3. Possibly use LNG, a fuel with relatively limited availability and not without its own required investment costs.
4. Or engage in using the ‘new kid on the block – very low sulphur fuel oils (VLSFOs)?
Many ship owners and operators did not openly declare their strategy and fuel choice until well into the second half of 2019 and it was at this time VPS really started to see VLSFO samples coming into our laboratories in increasing numbers. The immediate observations at that time regarding VLSFOs were in relation to a wider range of densities and viscosities, higher levels of cat fines, numerous stability and cold-flow issues and the fact that even though these fuels were meant to ensure compliance to 0.50% sulphur content, 10% of samples tested were found to be non-compliant in terms of sulphur. By the end of 2019, VPS identified 8% of the VLSFO samples tested had a sulphur level greater than 0.50%, having tested almost 5,000 VLSFO samples at that point. After 1 January 2020, VPS witnessed an immediate and significant switch to VLSFO fuels in the marine fuel supply and demand market, with an average of 67% of all bunkered fuel tested by VPS being VLSFOs, over Jan-Apr 2020. During this period MGO market share was at 16% with HFO at 15% and ultra-ULSFO at only 2% (See Figure 1).
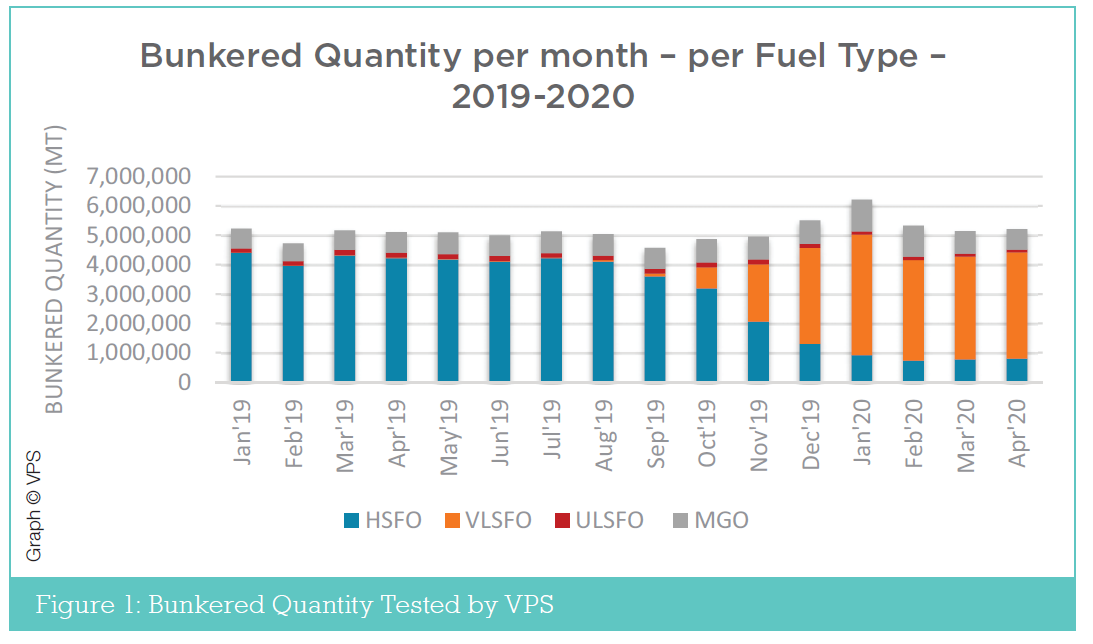
Whilst the year started very strongly for bunkering volumes, the COVID-19 pandemic played a significant role in decreasing bunker fuel demand in March and April, however the percentage increase in VLSFO demand continued against other fuels. The fall in crude pricing and subsequent marine fuel price drop, did not see a rise in demand for MGO, or a fall in demand for HFO, as one may have expected. However, media reports of some shipping companies postponing scrubber installations whilst cheap fuel was available does appear to have occurred over this time period. Reviewing VPS Bunker Alerts as an indicator of overall fuel quality (these are reports of short-term fuel quality issues in specific ports for specific test parameters), VPS issued 23 Alerts between January-April 2020 as compared to only 9 Alerts over January-April 2019. Interestingly there has been an increase in Bunker Alerts for MGO, HFO and VLSFO this year as in Table 1:
These figures highlight that there has been an increase in quality issues for all marine fuel types to date in 2020.
VLSFO – Quality
VLSFO Off-specifications
For VLSFOs, which are the most commonly purchased marine fuel-type in 2020, 4% of these fuels exceed at least one test parameter specification, with sulphur accounting for 25% of those off specification parameters, followed by TSP (i.e. stability) issues at 13% as in Figure 2.
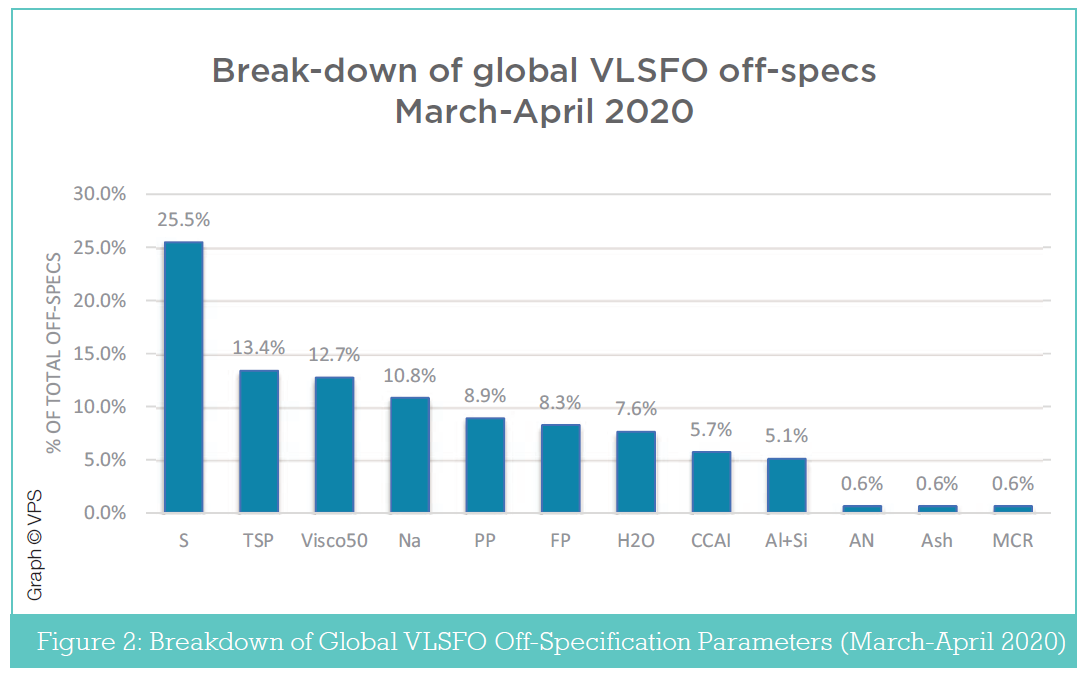
VLSFO Compliance
In terms of sulphur compliance, VLSFOs have shown a significant improvement from the 8% non-compliant level at the end of 2019, with only 1.1% of samples exceeding 0.50% sulphur over March-April 2020. In terms of the 95%-confidence limits, 44.3% of samples fall between 0.47%-0.50% sulphur, 0.8% of samples were between 0.51%0.53% sulphur, with only 0.3% of samples tested exceeding the upper limit of 0.53%. For all of the main bunkering regions VPS are seeing the average sulphur levels at compliant levels, but on occasion, some significant maximum spikes up to 1.43% sulphur (See Figure 3).
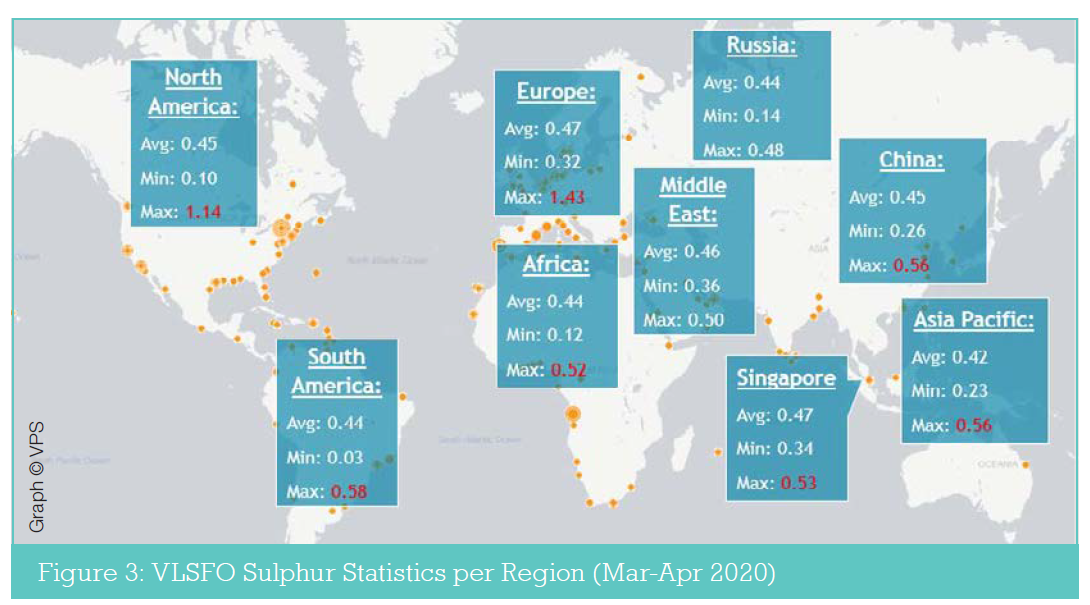
VLSFO Stability
Since VPS first began testing VLSFOs, stability has been an area requiring additional consideration. VLSFOs are highly blended fuels containing varying amounts of aromatic and paraffinic components, which creates a greater potential for the fuel to destabilise, forming asphaltenic sludges, waxes, or both. These stability issues require greater attention regarding the fuel’s storage conditions, transfer and burning, following receipt onboard, in order to avoid operational problems. Although TSP accounted for 13% of the VLSFO off-specifications between March-April 2020, the average Total Sediment Potential (TSP) values across the world’s bunkering regions are on specification with values between <0.01%-0.03%. It is noticeable that VLSFOs have been tested as stable when bunkered, but have quickly become unstable, some within only a few weeks, indicating their storage lifespan is much shorter than the more traditional marine fuels (See Figure 4).
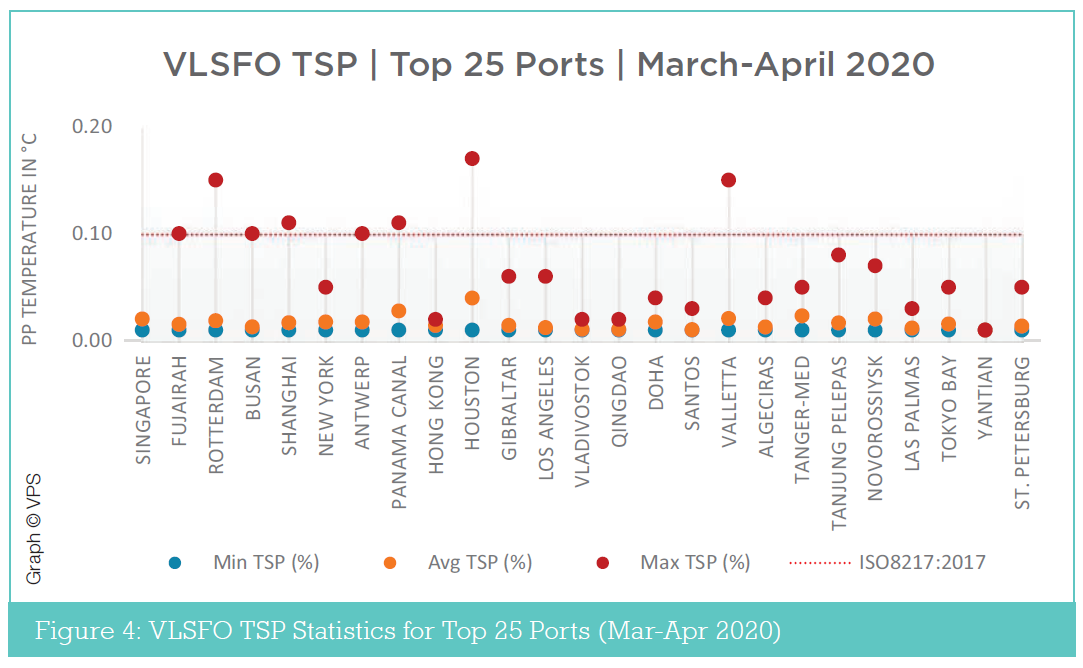
Cold-flow properties are another concern with regard to VLSFO stability. Due to higher paraffinic content within VLSFOs, there is an increased potential for the fuel to precipitate wax. Maintaining the fuel above the Wax Appearance Temperature (WAT) ensures the fuel will flow freely. However, the latest data has shown the average WAT is 22°C greater than the Pour Point (PP). Therefore, traditional industry advice of storing fuels at 10°C above the fuel’s PP is no longer a trusted guideline, as the fuel may produce wax at a much higher temperature than +10°C >PP. Although the majority of VLSFOs are exhibiting PP<30°C more than 75% have WAT >30°C. In addition, if a fuel has precipitated wax, the temperatures required to dissolve that wax, Wax Disappearance Temperature (WDT), is on average 11°C higher than the WAT, with more than 85% of VLSFOs having a WDT of >40°C. Therefore, WAT/ WDT/PP are key operational parameters in avoiding waxing of VLSFOs (See Figure 5).
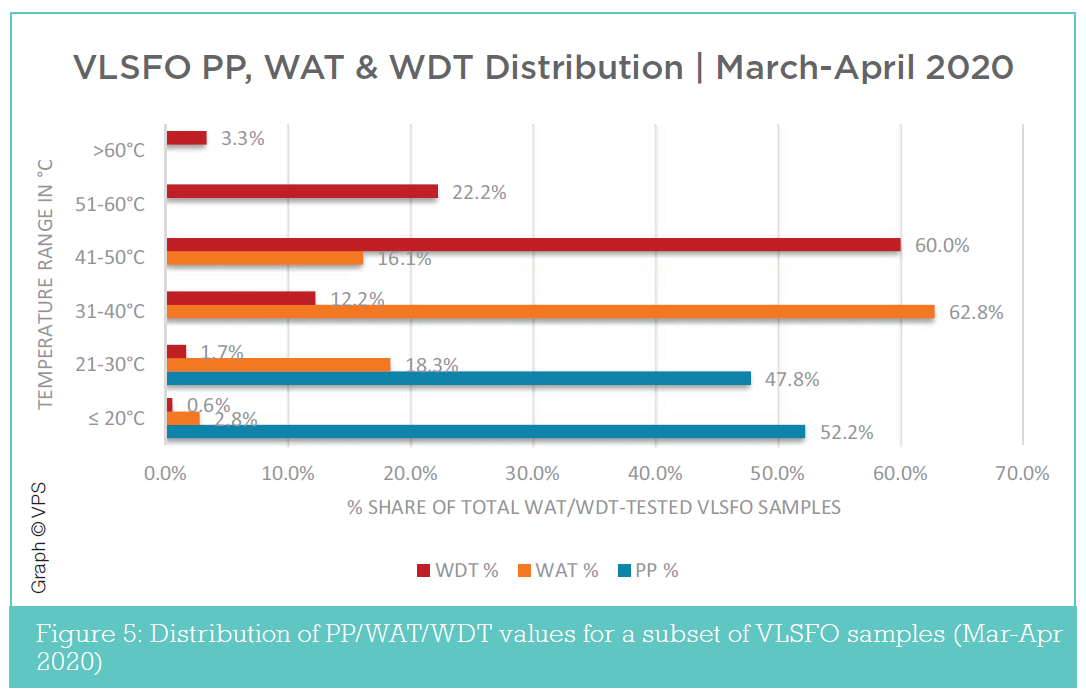
VLSFO Sludge Generation
As stated, VPS has observed a sharp increase in the number of operational issues due to excessive sludge generation onboard vessels. This is a global trend, concerning fuel deliveries made by multiple suppliers in multiple ports and geographies. Operational issues encountered include abnormal purifier operation, blockage of filters and blockage of auto‐clean backwash filters. Sludge formation can be caused by a combination of hydrocarbons, asphaltenes, resins, paraffins, water, sediments and biomass produced by bacteria and oxidized or polymerized material. There are several potential causes of these issues, including:
1. High WAT/WDT: VLSFOs with high WAT/ WDT and high cat fines create a need to operate separators at higher temperatures, at shorter discharge intervals. When this is not done, wax starts to form, affecting purifier operation as well as clogging the fuel system’s filters. Service and settling tanks also need to be maintained at higher temperatures than usual.
2. Contamination: VLSFOs with high WAT/ WDT that also have chemical contamination, followed by low viscosity, can likely not be handled onboard vessels. In these cases, the only solution is de-bunkering.
3. Incompatibility: VLSFOs that are incompatible can cause separator sludging and clogging of filters. This is not immediately apparent through testing the ISO8217 suite of parameters. It has been important to clean the bunker storage, settling‐ and service tanks completely when switching overto VLSFO fuel. VPS has observed that the majority of the vessels have adhered to these recommendations and have successfully changed over from HSFO to VLSFO. However, several incompatibility issues have been reported when the vessel changes over from MGO to VLSFO (or vice versa). The consequence of such issues becomes critical especially when the vessels are approaching or leaving port or in restricted waters.
4. Unstable blends: Some of the VLSFO blends appears stable when bunkered but become unstable over a short time period. Heating the fuel in the tanks (to maintain suitable storage and transfer) and purifiers (to achieve efficient purification) deteriorates the fuel’s stability and fastens the ageing process, as illustrated in Figure 6.
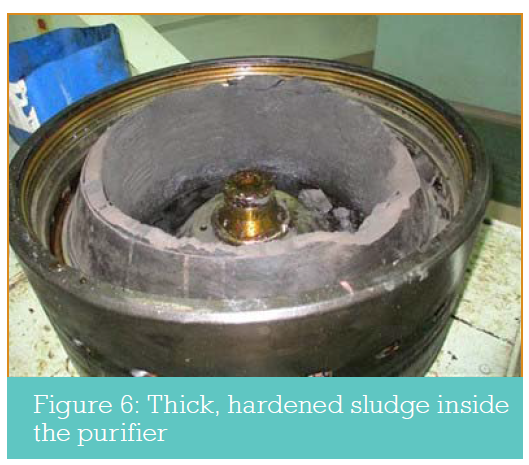
VLSFO Catalytic Fines
From the outset, VLSFOs have exhibited higher cat-fine levels than HFOs. However, more recently, VLSFO cat‐fine levels have reduced quite significantly across all major bunker regions. No extremely high catfines were observed in April 2020, indicating a more consistent and higher quality VLSFO supply. Globally, the number of VLSFO samples with Al+Si > 60 mg/kg has been reduced to only 0.1% in April 2020. Regionally, there are still some high cat‐fine VLSFOs supplied, but this is less of an issue than at the beginning of 2020, when high cat fines were quite common for VLSFOs.
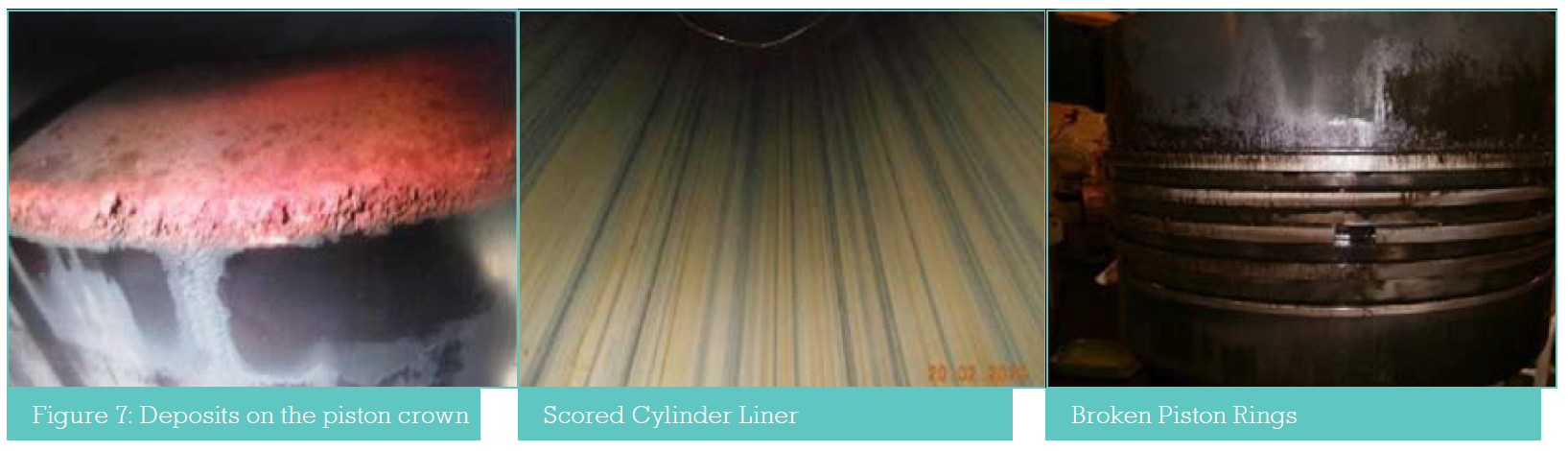
VLSFO & Lubricating Oil
VPS has identified significant engine damage arising in more than 40 vessels over the past few months. This engine damage has been in the form of hard, abrasive deposits on piston crowns, excessive cylinder liner wear and broken piston rings (Figure 7). As a consequence of this damage, VPS undertook a comprehensive investigation. The investigation identified that the reserve Base Number (BN) in the cylinder oil was not being utilised to neutralise the acids formed during the fuel combustion process as is its purpose. This resulted in calcium compounds being deposited on the piston crown, which became hard and abrasive causing the liner wear, liner scuffing and piston ring breakage resulting in serious operational issues. It is worth noting that in general, when the BN is reduced, the lubricating oil detergency reduces and the oil film is lost, whereas when the BN increases, the detergency improves and the oil film is retained but then deposit formation starts. A number of preventative actions may be taken by ship operators using VLSFOs to protect engines and avoid operational issues arising from excessive liner wear. Primarily, undertaking VPS Cylinder Scrape-Down Analysis will identify if an adequate lubricating oil formulation is being used, which may be further confirmed by a VPS Sweep Test. In addition to this, the ship operator should closely monitor engine operation during introduction of new VLSFO fuel and changeover of VLSFO to MGO and MGO to VLSFO when entering/leaving ECAs.
Summary
So, shipping boldly stepped into the unknown of IMO 2020 to meet the challenges headon. The market embraced VLSFO fuel as the predominant fuel of choice and this fuel currently accounts for 70% of global marine fuel supply and demand. COVID‐19 brought a major threat to the world’s health, but also to global business, with shipping being no exception. Yet one outcome, that of falling fuel prices, did not cause an increase in demand for MGO, or a decrease in demand for HFO. However, VPS has issued a significant increase in bunker alerts in 2020 versus 2019, for VLSFO, MGO and HFO, indicating poorer quality fuel across the supply chain. Despite this, sulphur compliance and cat‐fine levels within VLSFOs have shown continuous improvements, as we’ve progressed through 2020. However, the most frequent issue with VLSFOs continues to be their stability, in relation to sediment potential and cold‐flow properties. It has also been noted that the shell‐life of VLSFOs is shorter than both HFO and MGO. Added to the additional fuel management considerations VLSFOs require, the lubricating oil base number, is also a heightened concern when using VLSFOs, in avoiding engine damage. One closing thought: Remember that shipping has had over 50 years of HFO/ MGO experience, yet only five months of VLSFO experience...as an industry, it’s a case of STILL LEARNING!
For more information please contact Steve Bee at steve.bee@vpsveritas.com