OCM - Water contamination in a marine lubricant environment
Article by Paul Parkinson - Global OCM Business Development Leader
Water is known the world over as a key substance to life on earth. Put simply, the life of our planet and all living things residing upon and within it, are highly dependent upon water. Yet in the world of engines, machinery and lubricants, the total opposite applies where water can lead to the death of mechanical assets, or at least their failure to operate, or the lubricant to be effective.
This article aims to explain;
• Problems associated with water in a marine vessel lubrication environment,
• The use of Oil Condition Monitoring (OCM) as an effective means of identification and quantification
• The different types of OCM tests for water available and
• Prevention and Potential solutions
Where does water contamination come from?
It is easy to see the potential for seawater ingress in a maritime environment. However, fresh water can also present a problem, entering via condensation or leakage from cooling or heating systems. Water (either fresh or saline) can exist in any one of three forms; dissolved, emulsified or separated.
What problems are associated with water contamination in lubricating oil?
Even at low concentrations (0.1-0.2%) water can compromise the purpose and effectiveness of lubricants. Lubricating oils have a vital part to play in the marine world and industry in general as they are designed to reduce friction and wear, cool parts, form seals, as well as absorb shock loads, dampen noise, transport energy and act as cleaning agents.
CIMAC (the International Council on Combustion Engines) states in its Publication 30 Used Oil Engine Analysis – User Interpretation Guide, “Water affects the viscosity and lubricity of the lubricating oil and if not removed it may form an emulsion.” Noria Corporation (Lubrication and Oil Analysis Training Organisation) in their “Best ways to test water in oil” tell us that “bearing life can be reduced to less than 25%, if water is present in quantities as low as 1000ppm (0.1%).”
Water can cause the formation of acids, sludge and varnish, leading to corrosion (rust) and damage to bearings and other engine parts. Furthermore microbes can flourish in the presence of water leading to corrosion in storage tanks and pipes and potentially blocked filters.
How do we monitor for water presence?
Oil Condition Monitoring (OCM) utilises the science of tribology and monitors the condition of both lubricant and machinery and has an important role in preventive maintenance programmes. The best analogy is that of a blood sample taken by your doctor to identify, predict and help combat any potential health issues. Water analysis in oil is considered one of the most important OCM tests to perform.
Like any testing programme, taking the sample is a key and fundamental part of the monitoring process. It is important therefore that the contents of any sampling kit used, are easy to use and practical. A representative sample taken in the correct fashion with the appropriate container is vital to receiving a meaningful result. Using a container which has been used previously, will more than likely affect the analysis, challenging the integrity of the analysis and any resulting advice.
Information relating to the sampling location, type of lubricant and operating hours, are key and must be recorded to facilitate a comprehensive report. Furthermore the initial sampling stage is also very helpful in terms of identifying a potential problem as the sampler will be able to see if water is present through the lubricant exhibiting a milky or cloudy appearance.
What are the best laboratory tests for water?
On-board sampling kits are a convenient initial solution but, given the low levels of detection required, they certainly have their limitations. Water does not always emulsify and it can dissolve in low concentrations, where such levels would be below the limit of detection of such portable kits. A more sensitive and sophisticated analytical laboratory solution should always be considered in order to confidently establish the presence of low levels of water. Further to this there are a number of analytical procedures available and each employs a different technique. It is important to understand the limitations of each technique before acting upon a value. The different tests available are summarised in Table 1.
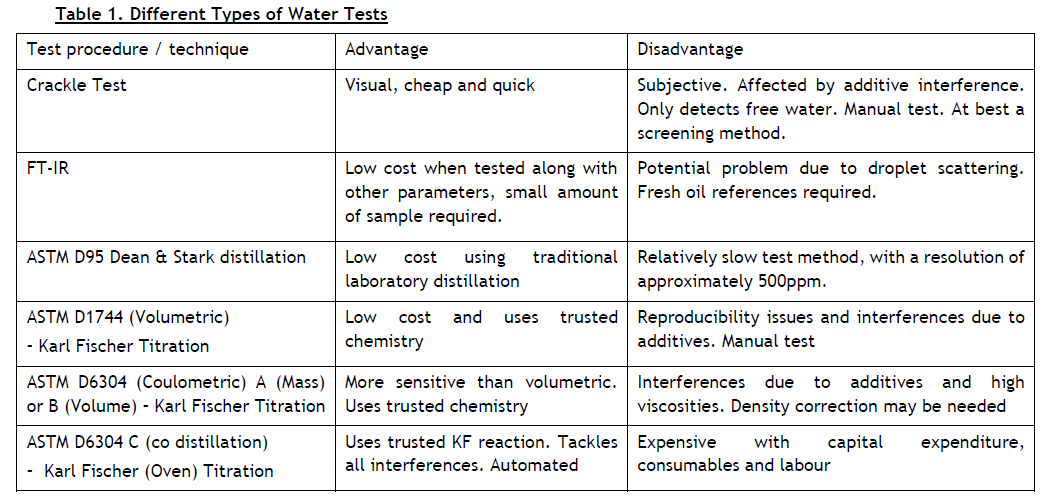
In summary, crackle and FT-IR methods are useful screen techniques but should be used with caution given their respective technical frailties. It is regarded by many that the best procedure from an analytical perspective is the Karl Fischer (KF) reaction which is selective to water and is able to measure all three forms. The Coulometric technique is more sensitive than the volumetric one. The volumetric technique is reliable at points of a percent level, yet coulometric KF can detect water down to low ppm levels. The additional distillation step provided through ASTM D6304 C (using an oven accessory) gives even greater reliability as it avoids additive interferences and it is only the water that is evaporated and eventually measured. Detection levels can be down to as low as 50ppm.
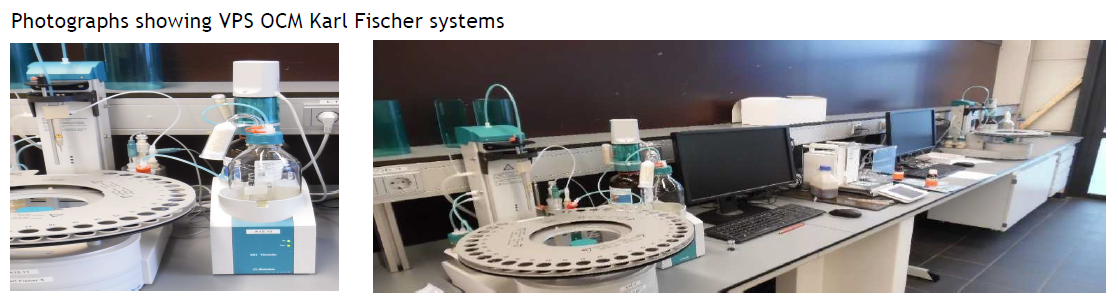
It is worth noting that the temptation to use the crackle test can create a multitude of problems. This test centres on water crackling (spitting) when in contact with a hot surface. It is simple, inexpensive and fast, so satisfies certain important criteria. Unfortunately, it is also very subjective, only responds to free water and is affected by additives that may be present.
Any other issues around water testing and reporting that we should be aware of?
Industry standard (e.g. ASTM) test procedures will expect results (as %) to be reported to a given number of decimal places. For ASTM D6304 C this is two decimal places. This could lead to potential rounding errors, that being the difference between the actual value and the rounded up value.
There are also two important scientific definitions that need to be explained. In an ideal world if a specified test procedure is performed by any lab, all results would be identical. The reality is somewhat different and “acceptable imperfections” are defined by the American Society for Testing and Materials (ASTM) as Repeatability (r) and Reproducibility (R) for each of their methods. Repeatability describes the range that an obtained result differs or may differ from the true value if the analysis is performed on the same date by the same test method and equipment on the same test material, by the same analyst. Reproducibility describes the range that an obtained result differs or may differ from the true value if the analysis is performed on the same test material by the same test method, but under different circumstances, ie different laboratory, different equipment and different analyst. Obviously, different circumstances cause greater variation in the results, and therefore, the reproducibility range will be wider than the repeatability.
What does Rounding, Repeatability and Reproducibility mean for Water Content and testing in general?
As a general guide VPS use 0.2% water in 2 stroke/ 4 stroke engines as a warning level while hydraulic systems and gearbox are triggered at 0.1%. Results above these values are considered to be critical and action should be taken immediately. Engine manufacturers state similar values; MAN B&W criteria for cleaning / exchanging of lubricating oil is 0.2 % (max 0.5% for a short limit), MAK says 0.2 % and Wartsila states 0.3 % as a “condemning” limit.
This means that a two decimal result (from ASTM D6304C) when rounded to one could trigger a stated limit. Furthermore because of the repeatability and reproducibility effects a result should not always be seen as a single figure when comparing with a guideline (or data from another lab) but needs to be understood as within a calculated range of the value provided.
This may seems a complex situation and to help unravel the potential confusion and difficulties around these three R’s, you should always consult with your OCM supplier. VPS provide this support from our in-house experienced laboratory personnel and our technical advisers/diagnosticians.
What can be done to prevent or minimise water presence?
Unfortunately, it is almost inevitable that there will be an ingress of water. It is important once identified that you perform a root cause analysis to establish its source and put any available measures in place to prevent or limit water ingress. In an engineering sense, centrifugation before separation or desiccant breather systems (if appropriate) will help minimise water ingress. Regular checking of seals will always be advantageous. These in addition to good hygiene are good, logical and sensible preventative approaches. Furthermore, lubricant companies include specific additive chemical compounds to combat water and enhance the base oil. Demulsifier additives are focussed on stopping the formation of an oil water emulsion, allowing free water to be more easily identified and dealt with. Biocides can also be added to prevent any damaging microbial activity. Whatever measures are used there will always be potential for water contamination in a marine environment. It is important that a predictive maintenance programme is in place to minimise the length of time of its existence to reduce the amount of damage as illustrated in chart 1. This chart shows that no intervention in terms of cost and risk is not a viable or sensible option. The US Department of Energy Federal Energy Management Program (FEMP) has estimated that a properly functioning Predictive Maintenance programme can provide between 30%-40% savings over a reactive maintenance programme and can;
• Reduce maintenance costs by 25-30%
• Eliminate breakdowns by 70-75%
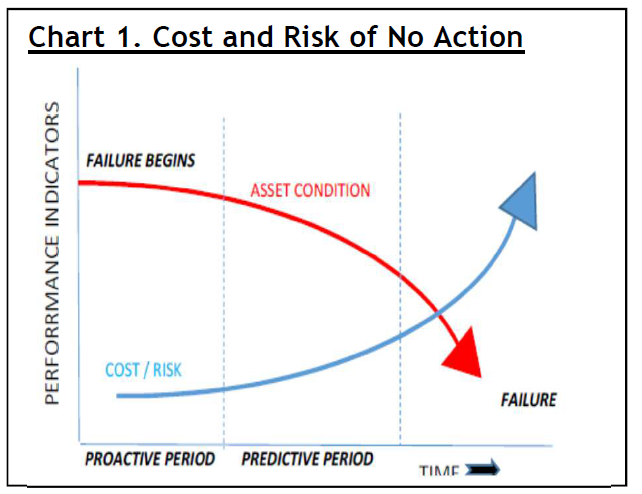
In conclusion, we should recognise the importance and value of oil condition monitoring and balance its relatively small cost against the enormous saving on replacement, repair or downtime. The benefits and savings of OCM are further enhanced when considering the significant changes to fuel and abatement technologies that will occur as a consequence of the 2020 legislation. Veritas Petroleum Services (www.v-p-s.com) are completely independent and impartial and are an international market leader in fuel and oil testing, inspection and advisory services. VPS has an important role in OCM and Fuel Testing preventive maintenance programs and our Rotterdam Laboratory has the very latest analytical technology, automation and robotics for the testing of lubricants and fuels.